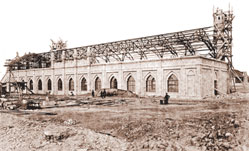
On 28 December 2010, the tap was turned on a new project to ensure that more citizens of Baku could celebrate the New Year with a splash, as well as the traditional bang.
The occasion was the inauguration of another pi peline across Azerbaijan. This time the pi pes were carrying water rather than oil or gas and the flow was towards, not away from, Baku. The Oghuz-Qabala-Baku water pi peline is now bringing water from high in the Caucasus mountains, in the north of the country, to slake the thirst of the capital’s growing population and industry. Two newly-constructed reservoirs feed the pi peline from 410 metres above sea level – their height ensuring that the 262 kilometres are covered without the need for pumps. The pi peline itself is made of Glass Reinforced Polyester (GRP), except for a 50 kilometre section of steel to withstand particularly high pressure, and is 2 metres in diameter.
This huge pi peline, built over 3 years, is expected to have a dramatic effect on the capital’s water supply. Before it came into commission, 60 per cent of the population only had water in their taps for a few hours each day. Expected to be in full flow during February, Oghuz-Qabala-Baku will reduce this figure to 25 per cent. And at the inauguration ceremony, President Ilham Aliyev said that additional projects – the Takhtakorpu reservoir and Absheron-Samur canal - were in hand to further improve the situation in Baku.
The whole project, including new pi pes, sewers and pumping stations in the capital, was financed from within Azerbaijan - 780.4 million manats from the State Oil Fund, which receives its income from the current boom in oil and gas.
One hundred years ago the first great project to bring water to the city of Baku – the Shollar pi peline – was well underway, and was also funded largely by oil money. Haji Zeynalabdin Taghiyev, who made his fortune in the city’s first oil boom, and initiated many philanthropic projects, put up most of the finance, but the city authorities turned to a British civil engineer, William Lindley, to bring the project to fruition. It was in its time one of the most ambitious engineering projects in Europe; from the Caucasus Mountains to the Absheron peninsula, some 18 years in process, hampered by outbreaks of revolution in the Russian Empire (1905), and by World War (1914), it was finally completed in 1917, the last year of its maker’s life. The Illustrated London News printed an article in 1912 about the project and (by then knighted), Sir William Lindley’s contribution:
WATER FOR A GREAT OIL – CITY: BUILDING THE LONGEST CONDUIT IN EUROPE
The construction of reservoirs and a conduit for the supply of water to the city of Baku constitutes an engineering achievement without parallel not only in Russia but in Europe. It is the scheme designed by and carried out under the direction of Sir William H. Lindley, M. Inst.C.E., F.C.S., whose work during the last forty years has made his name famous throughout almost every country on the Continent. At an age before most boys have seriously considered what profession they should enter, Sir William Lindley had already established his reputation as a civil engineer. Born in 1853, and educated privately at Blackheath, he matriculated at London University in 1869 (at the earliest possible age); he then, as a youth of seventeen, joined his father, Mr.William Lindley, under whose design and direction the waterworks of the city of Budapest were being constructed. Such ability did young Lindley display that from 1870 to 1873 he was entrusted with the work of construction as Resident Engineer.
The newspaper went on to review the remarkable career of this great British civil engineer. Before he was 30 he was Chief Engineer for public works of the German city of Frankfurt. He oversaw the construction of the water and sewerage system (designed by his father) for Warsaw. The cities of Prague, Tiflis (Tbilisi), Moscow, Amsterdam and Vienna were among the many who called on his expertise. In 1906 the British government appointed Lindley to be Assistant Commissioner on a Royal Commission to study the waterways of Belgium, France, Germany, and Holland, with a view to improving the canals of the United Kingdom. Following this work he was knighted. The article continued with details of the Azerbaijan project:
The construction of the Baku Waterworks will form an engineering record, consisting as it does of the making and laying of a conduit over a distance of 110 miles (the longest pipe – line in Europe) at the hitherto unprecedented rate of one mile per week. The pi peline will be large enough for a man to walk through, and is guaranteed to carry on the saddle twenty-five tons per metre, as minimum load. The conduit will be laid at an average depth of 25 ft. The carrying out of the manufacture and supply of the pipes of the pipes for the 110 miles of standardised 1.75-by-1.50-metre and 1.50-by-1-metre pipes has been entrusted to the Improved Construction Company Ltd., of 47, Victoria Street, London, S.W., the owners of the Jagger Patent Process of manufacturing plain and armoured concrete...... Hitherto, the best concrete has not exceeded a weight of 130-140 lb. per cubic foot. Concrete made by the Jagger patent process has a guaranteed weight of 156 lb. per cubic foot. High- pressure pipes (such as now being manufactured for the Baku Waterworks conduit), without lining or rendering of any sort produced by the Jagger process are asserted to be, dimension for dimension, six times stronger than any other pipe made in the world.... At the same time, the cost of labour in manufacture is reduced by ninety per cent, as the result of the simplicity and rapidity with which the concrete material, of the highest efficiency and for any purpose, is produced. The Company’s works at Fulham can claim to be the best-equipped and most up-to-date in the world. To carry out the contract on the Baku Waterworks the Company has built factories at Hatchmas and Devitche, on the line of the conduit. Here the 110 miles of piping will be manufactured. These factories will use daily, as raw material, 1,860,770 poods of cement, and 450 cubic metres of sand and clean gravel. By the Jagger process there will be effected an initial saving of £130,000 on the cost of the Baku Waterworks.
We raise our glasses (of water) to the innovators and technicians of the past and the present who perform miracles of engineering to bring us the ‘simple’ things in life.